Machine Design is the process of selection of the material, shape, size and arrangement of mechanical element so that the machine will perform its task.
A process which includes design of all parts of machine subjected to carry the forces without failure by transforming other form of energy into mechanical energy.
General Procedure in Machine Design:
- Need: Indicate the need for which purpose or aim the machine is to be used and design.
- Mechanism: Selection of suitable mechanism that will give the desired motion required.
- Analysis of forces: Finding the forces acting on each members of the machine.
- Selection of material: Selection of suitable material according to availability, cost and conditions for each member and suitable factor of safety.
- Design of element: Find the size of each member of the machine by considering the forces acting on the member and the stress.
- Modification: Modification is necessary of manufacturing to reduce overall cost modification of size of the member.
- Detail Drawing: Draw the detail of each component with tolerance and assembly of machine with complete specifications.
- Production: The components as per drawing are manufactured in the workshop.
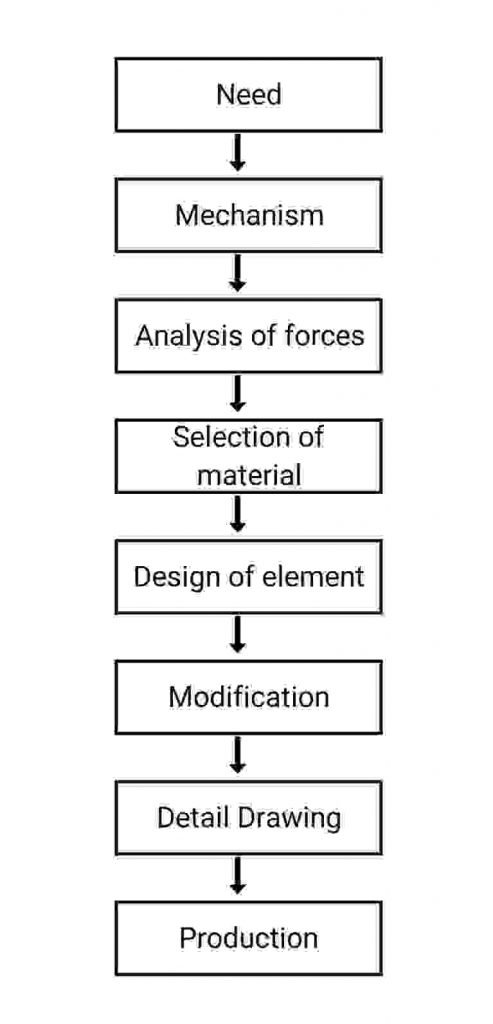
Mechanical Properties of Materials:
- Strength: The ability of material to sustain the load without breaking or rupture is known as strength.
- Fatigue: The property of material to resist the repeating load before it rupture is known as fatigue.
- Elasticity: The property of material in which a deformation is done under the application of load and it vanished after removing the load is called as elasticity.
- Plasticity: The property of material in which a deformation is done under the application of load but the deformation does not vanished is called as plasticity.
- Ductility: The property of material due to which the wires can be drawn under the tensile force is called as ductility. Examples: Copper, Silver, Gold, Aluminum, etc.
- Malleability: The property of material due to which the thin sheets can be drawn by rolling or hammering is called as malleability. Examples: Copper, Silver, Gold, Aluminum, etc.
- Brittleness: The property of material due to which it breaks into small pieces under the application of ultimate load without prior indication is called as brittleness. Examples: Cast Iron, Ceramics, Glass, Concrete, etc.
- Hardness: The property of material to resist abrasion, scratching, penetration or wear is called as hardness. Examples: Rockwell, Vickers, Brunel, etc.
- Toughness: The property of material to absorb the shock energy, this capacity is called as toughness. It is also known as impact strength. Examples: Shock absorbers, Springs etc.
- Stiffness: The ability of material to resist the deformation under the load is called as stiffness. It is also known as rigidity.
- Creep: When a machine component is subjected to a constant load at high temperature for long time it shows permanent deformation is called as creep.
- Resilience: The property of material to absorb the energy and to resist shock and impact loads is called as resilience. Examples: Springs, Toys, Wrist watches, etc.
Factor of Safety:
Factor of safety is defined as maximum stress to working stress or design stress.
For ductile material: Factor of safety is defined as the ratio of yield point stress to design stress.
Factor of safety = Yield Stress / Design Stress
For brittle material: Factor of safety is defined as the ratio of ultimate stress to design stress.
Factor of safety = Ultimate Stress / Design Stress
Selection of factor of safety: It depends upon number of consideration such as material, type of stress, mode of manufacturing. The factors to be considered while selecting the factor of safety are as follows:
- Effect of failure on human safety and financial loss.
- The reliability of applied load.
- The reliability of the properties of material.
- Quality of manufacturing and service conditions.
- The extent of localized stresses.
- The extent of simplifying application.