In Electrical Discharge Machining (EDM) process, the tool electrode having particular shaped, but in wire cur electrical discharge machining (WEDM) the tool electrode having a thin wire.
As the material removal is obtained continuously in the feed of the workpiece is called as wire-cut electrical discharge machining.
What is Wire-Cut EDM?
Wire-Cut Electrical Discharge Machining (WEDM) is an electro thermal production process in which a thin metallic wire along with the de-ionized water allows the wire to cut through metal by the use of heat from electrical sparks. The wire is usually made of brass or stratifies copper and the size in between 0.02 and 0.33 mm in diameter.
Also Read: Electrical Discharge Machining (EDM)
Working Principle of Wire-Cut EDM:
Figure shows the working principle of wire cut electrical discharge machining. In this type of machining the wire is used as the form of tool electrode.
It is very thin wire of diameter 0.05mm to 0.25mm. The wire is connected to the negative terminal and workpiece is connected to the positive terminal of the DC power supply same as the working of electro discharge machining. The dielectric is calculated to the storage of tank at high pressure pump. The spark can be generated due to current flowing from a wire and the process is done.
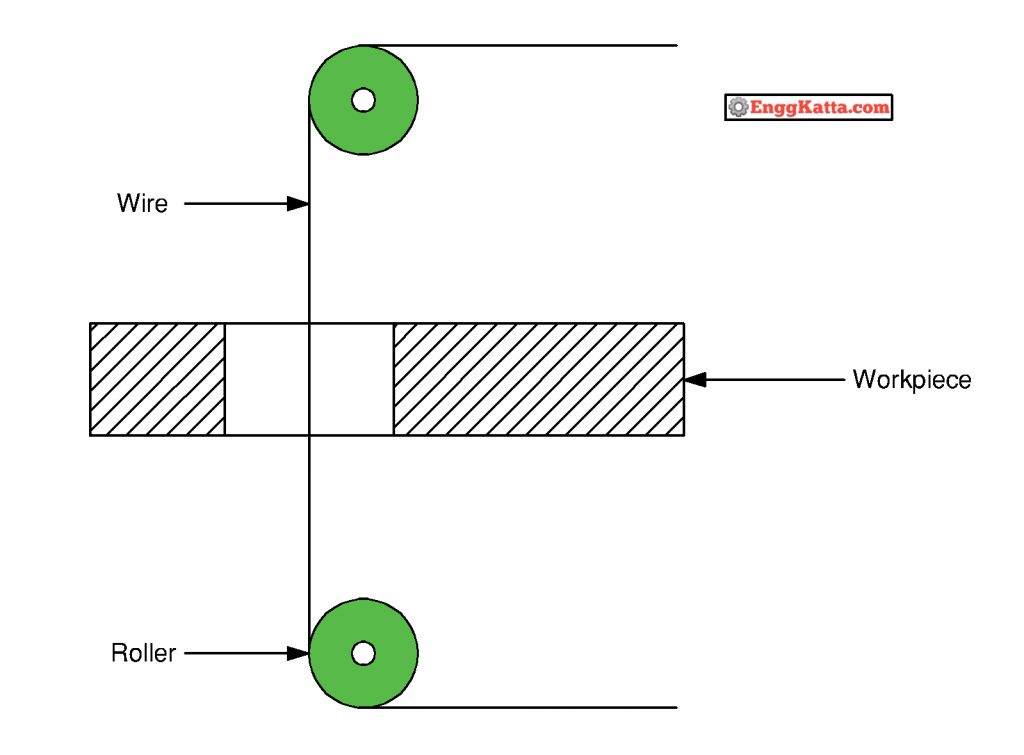
Controlling Parameters of WEDM:
Following are the controlling parameters of wire-cut electrical discharge machining are as follows,
- Discharge Current: The discharge current in between 20 to 30 amperes.
- Duration of pulse: The high duration of pulse goes produce more removal rate and low duration of pulse produce low removal rate.
- Frequency of pulse: The frequency of pulse in between 50KHz to 1MHz.
- Wire Diameter: The diameter of thin wire is 0.05mm to 0.25mm.
- Wire Speed: The speed of wire is about 5 to 200 mm/sec.
Advantages of WEDM:
Following are the advantages of wire-cut electrical discharge machining are as follows,
- It gives high accuracy.
- There is no need of storage of tool is required.
- There is low operating skill is required.
- Smooth complex surfaces can be possible to machining.
- A good surface finish can be obtained.
Applications of WEDM:
The following are the applications of wire-cut electrical discharge machining are as follows,
- It works for production of prototypes.
- It is used for making of stamping dies, drawings, extrusion tools, etc.
- IT is used for making blanking dies, plastic molding dies, stamping dies, etc.
- It is used for gauges, cam discs.
- It is used to machining larger parts that need to hold accurate tolerances.
- It is also used for making of small series of spare parts.