Laser Beam Machining (LBM) – Working Principle, Applications, Controlling Parameter, Advantages and Disadvantages
What is Laser?
Laser stands for light amplification of stimulated emission by radiation.
Laser is an electromagnetic radiation which produces monochromatic light in the form of beam.
The laser works on the principle of conversion of electrical energy into light energy then in the form of energy of thermal energy.
The light is generated in the lamp by ruby rod and the reflections are get on the lenses and the lenses are get the focus of laser rays on the workpiece. Due to the machining of the workpiece is done.
What is Laser Beam Machining?
A laser beam machining is a non-traditional machining process in which the machining is operated with the help of laser light. The laser light has maximum temperature strikes on the workpiece to melt dur to high speed. This process uses thermal energy to remove metallic or nonmetallic surfaces.
A laser beam machining works on the basic principle of laser, in which a laser beam is use as a monochromatic high intense light which can easily cut metals and non-metals. This machining process is widely used in sheet metal cutting.
Working Principle of Laser Beam Machining:
Laser Beam Machining works on the principle of conversion of electrical energy of flash lamp into heat energy to emit the laser beam by pumping the energy.
Laser Beam is focused on a lens to give high energy to helps the melting of metal. It works on the principle that when a high temperature laser beam strikes on the workpiece, the metal starts melting due to high temperature and high speed.
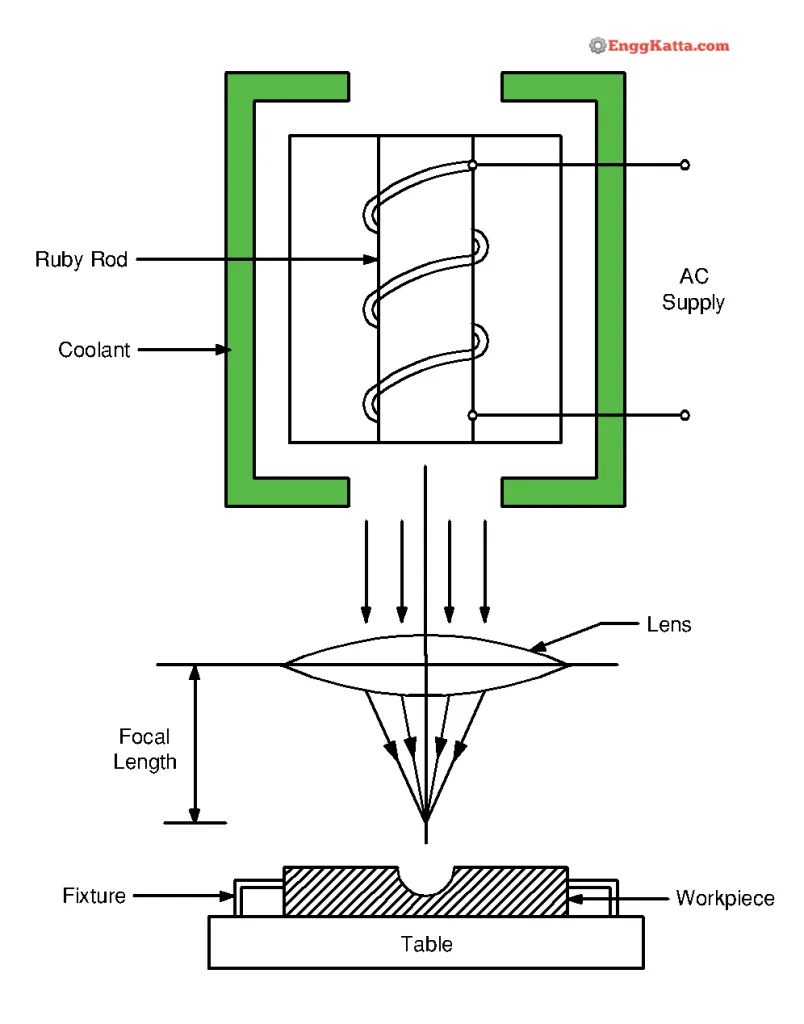
The high frequency of monochromatic light will fall on the surface then heating, melting, and vaporizing of the material. The setup and working of laser beam machining are as follows,
- Laser generation unit.
- Focal length.
- Cooling arrangement.
- Workpiece table and lens.
Equipment’s and Main Parts of Laser Beam Machining:
Power Supply:
A high voltage power supply is required for laser. The power is supplied to the system for exiting electron. The electron gets excited and ready to work.
Flash lamp:
Flash lamp is used for providing white and coherent light.
Workpiece:
The workpiece is used widely in this machining process is cutting sheet metal for manufacturing.
Read Also: Electro Discharge Machining (EDM)
Characteristics of Laser Beam Machining:
Following are the main characteristics of laser beam machining,
- It is not suitable for reflective materials.
- There is no physical contact between tool and workpiece.
- Complex shaped material can be produced.
- Low material removal rate.
- Machining of small holes can be possible.
Controlling Parameter of Laser Beam Machining:
- Intensity of laser beam: The intensity of laser beam is about 100000 kw/cm2.
- Pulse duration of laser beam: The pulse duration of laser beam is at 6 to 12 pulse/min.
- Focal length: The focal length is the distance between tool and workpiece.
- Mode of laser operation.
Advantages of Laser Beam Machining:
Following are the advantages of laser beam machining,
- The process has the ability to engrave and it can be drilled of micro holes.
- There is no burr or chips are produced in this machining process.
- There is no physical or direct contact between equipment and workpiece.
- Low wear rate.
- Low material removal rate.
- Complex surface can be produced.
Disadvantages of Laser Beam Machining:
Following are the disadvantages of laser beam machining,
- There is low of material removal rate.
- It cannot work on reflecting material.
- The flash lamp has limited life.
- Material holes may be taper from entry to exit.
- The laser beam machining requires High cost and high maintenance cost.
Applications of Laser Beam Machining:
Following are the applications of laser beam machining,
- Laser Beam Machining can be used for engraving of materials.
- It can be used for drilling of micro holes.
- It is used to drilling holes of jet engine.
- It can be used for laser heat treatment.
- It can be used for surgery of medical.
- It can be used for electronic field in communication devices and printers.